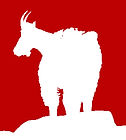
SEDY ENGINEERING
CO
DESIGN | SIMULATION | CONSULTATION
Sustainable engineering solutions for an emerging global economy.
Sedy Engineering CO is commited to finding solutions to engineering problems in struggling communities. We believe that being part of a global community means that our solutions shouldn't come at a cost to our neighbors' way of life.
Design Requirements
In order to be functional and fulfill the need of this project, the gondola must meet these requirements:
-Must be no larger than 15 inches in width, 2.5 inches in height, and 12 inches long.
-Must contain all electrical components internally.
-Must weigh less than 206 g.
-Must be able to withstand at least 1lb pressure applied at the end of the motor pylons.
-Must house a cargo release mechanism.
-Must be able to hold at least 1g of ballast.
-Must be compatible with the curved shape of the helium bladder.
-Must be constructed from ABS plastic.
-Must be black or white in color.
-Must have a master ON/OFF switch clearly marked
Parameters of Interest
The parameters pertaining to the performance of the gondola that will be specifically measured are:
-Weight
-Maximum forward speed
-Ability to drop cargo correctly
-Ability to support 1lb weight from end of motor pylon at any angle
-Run time at full throttle
-Door strength
-Time taken to navigate the competition course
The scoring rubric will be used to create a numeric score that will allow this device to be ranked against other devices that also completed the course.
Predicted Performance
The efficiency of the UAV will be found by competing in a timed even against other UAVs designed to meet the same requirements.
-It will translate through the air at 5.4 ft/s
-Gondola will weigh 202g
-It will successfully negotiate the obstacle course, drop the payload at the target, and exit the course by following a flight path similar to its entrance
-It will be capable of 20 minutes of continuous operation at full throttle
-The motor pylons will be able to withstand a 1lb load applied in any direction at the end furthest from the body.
-The cargo bay doors should be able to withstand the full torque (2.5 kg-cm) of the servo if an object were to become stuck in the doors and prevent them from opening or closing.
Actual Performance
The efficiency of the UAV will be found by competing in a timed even against other UAVs designed to meet the same requirements.
-Top speed: 2.25 ft/s
-The helium bladder provided 210g of lift force
-The UAV successfully negotiated the obstacle course in 334 seconds, dropped the payload at the target, and exited the course by following a flight path similar to its entrance
-The gondola was run at full throttle for 22 minutes before any noticeable drop in performance.
-The motor pylons were able to withstand a 1lb load applied in any direction at the end furthest from the body.
-The cargo bay doors was able to operate correctly and was not damaged when it was actuated while the UAV was on the ground.
-Actual Gondola Weight: 172g

Conclusion
The testing was successfully completed according to schedule. The UAV and course were prepared in advance to ensure that the audience would not be kept waiting. The UAV was filled with helium, trimmed, and allowed to make practice runs of the course before the actual test.
The performance of the UAV did not meet the expectations of the designers. This is partly due to an improper choice of motor controller. Airplane-type controllers were used instead of helicopter or car-type controllers, which allow the motor rotation to be reversed. This would allow the UAV to use “skid” steering, similar to a bobcat excavator. Without the reverse function, the turning radius of the UAV was poor and unpredictable. It depended on a great number of variables, including the forward speed, the duration of the pulse of power to the motor, and the air currents within the room.
The cargo drop mechanism functioned flawlessly and was able to deliver the payload to the target with no complications. Part of the requirement of the test was that the UAV not touch the target area while the payload was being deployed. This specification was also met with success.
The maximum forward speed was less than expected. This is due in part to the shortening of the propeller blades to fit within the propeller guards. These guards were necessitated by the rules of the ASME competition.