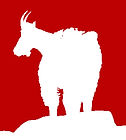
SEDY ENGINEERING
CO
​DESIGN | SIMULATION | CONSULTATION
Sustainable engineering solutions for an emerging global economy.
Sedy Engineering CO is commited to finding solutions to engineering problems in struggling communities. We believe that being part of a global community means that our solutions shouldn't come at a cost to our neighbors' way of life.
Project Details
Click through the slideshows for a summary of each project
Senior Project: Lighter-than-air UAV Gondola
​​
Unmanned air vehicles (UAVs) are less expensive and safer to operate than traditional aircraft. A need has been demonstrated for a UAV that is lighter than air, capable of precision maneuvers, and able to carry a payload. Lighter than air UAVs are inherently more safe to operate than their heavier than air counterparts because if there is a sudden failure of their electronic or radio system, they will not fall out of the sky. The American Society of Mechanical Engineers (ASME) has put forth this project as part of a Student Design Challenge. This project is being approached as a team. The members of this team include Mr. Patrick Kinney and Mr. Joe Sedy. Mr. Joe Sedy is responsible for the design, analyses, and construction of the gondola and its mechanical subcomponents.

This view shows the path the cable will follow through the plug. It is designed for 4mm OD shifter cable housing.

The finished end plug easily pressed into the aerobar, and the cables fit snugly but are easily fed through. The down turned angle of the cable as it exits the plug lowers friction that could be caused from a tighter bend in the cable. The end of the plug is embossed with the Sedy Engineering goat!


This view shows the path the cable will follow through the plug. It is designed for 4mm OD shifter cable housing.
Bar end plugs with internal cable routing
​​
A used pair of aero bars for a time trial bicycle came without end plugs. A standard sized plug was not available, so an end plug was designed that allowed the shifter cables to be routed through the aero bar and exit at an angle that wouldn't cause a small radius bend in the wire. The plug was created with SolidWorks, printed on a Dimension uPrint Plus printer, and painted with black spray paint. It is currently installed on the bicycle and serving it's purpose well!

SolidWorks render of final product.

SolidWorks CFD Analysis was used to optimize the nosecone shape for supersonic air speeds.

A scale prototype model was created for wind tunnel testing.

SolidWorks render of final product.
Argonaut Atmospheric Sounding Rocket
​​
This was a project for IET 265 SolidWorks at Central Washington University. A 6" rocket was designed to carry a 30lb payload to 60,000 feet. It was first created and tested in RockSim and then modeled in SolidWorks. SolidWorks Computational Fluid Dynamics analysis was used to select the best nosecone shape for the rocket. Click HERE for a PowerPoint presentation of the project.

SolidWorks render of beam and motor holder.
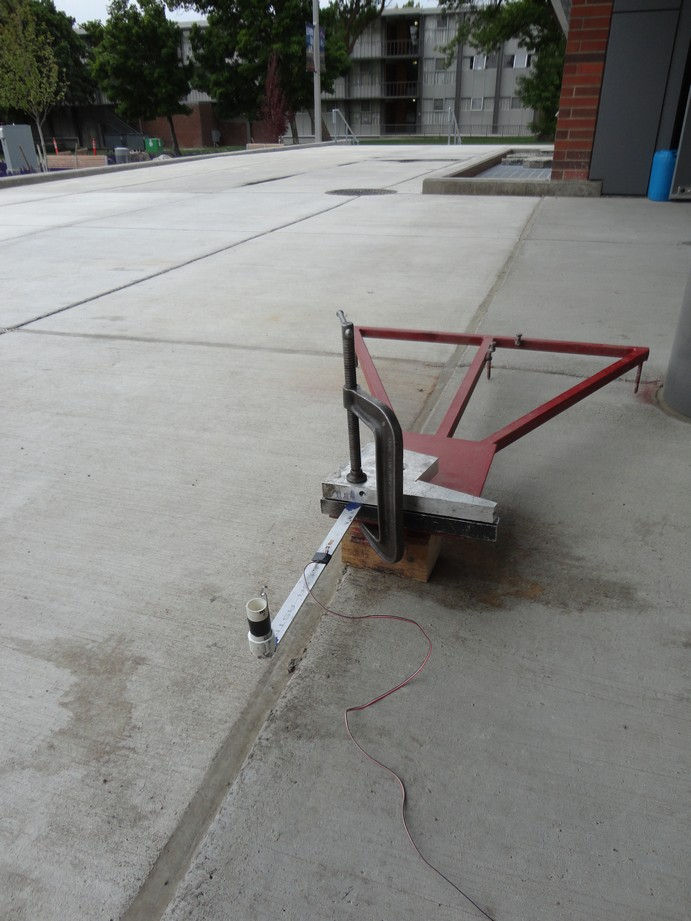
The aluminum is beam clamped in place and secured to large mass. The strain gauge is visible directly above the electrical tape securing the leads to the beam.
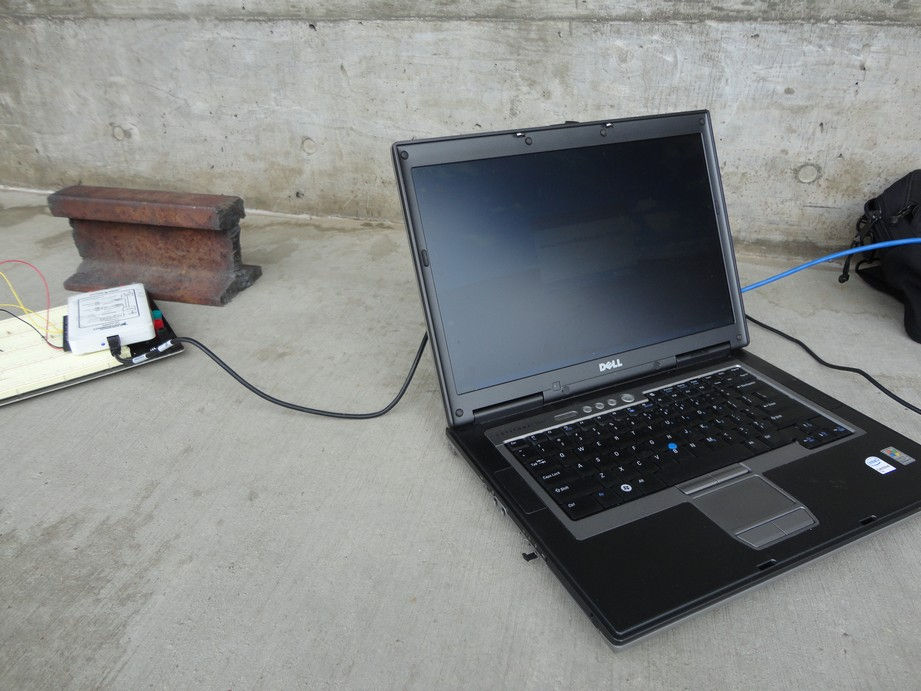
Ancient laptop running NI LabVIEW.

SolidWorks render of beam and motor holder.
Rocket Motor Test Stand
​​
This was a project for MET 426 Applied Strength of Materials at Central Washington University. The stand utilizes an aluminum beam to hold the motor in place. As it is being fired, the deflection of the bridge is measured using a strain gauge, an NI myDAQ, and NI LabVIEW. The deflection data was used to produce a thrust vs. time curve for each motor. Click HERE to be directed to a YouTube video of the testing, and click HERE to view a PowerPoint presentation of the project.

This is a AutoCAD sketch of the basic components of a bicycle frame.
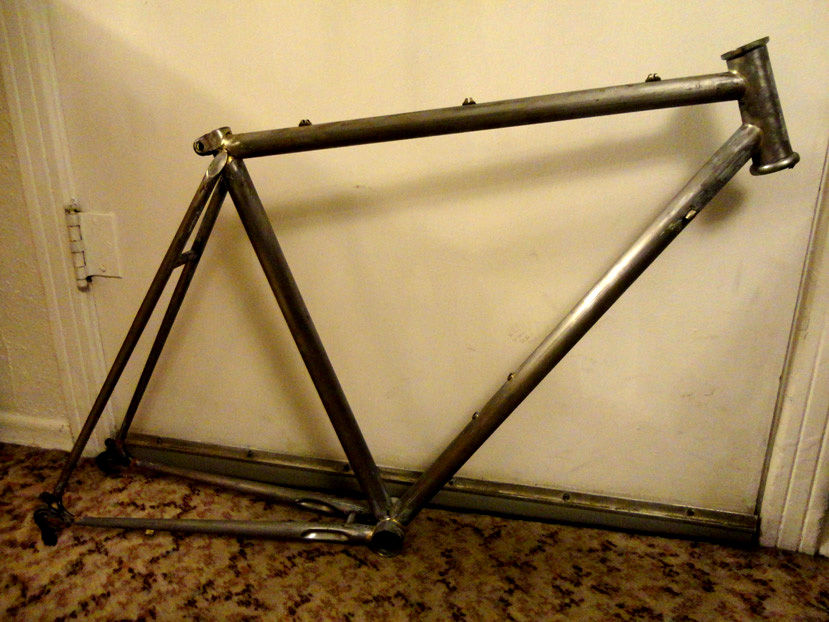
This is the actual Peugeot frame to be analyzed. It has been stripped down to the bare aluminum so it can be repainted.

This bike was a surprise for my wife's birthday, and this its inaugural ride on the Wenatchee Apple Loop. Looks like it's a winner!

This is a AutoCAD sketch of the basic components of a bicycle frame.
Bicycle Frame Static Stress Analysis
​​
This was a project for IET 311 Statics at Central Washington University. The static forces in the frame due to the weight of a rider and the reactions at the axles were to be determined. The frame is from an early 80's Pugeot bicycle I was in the middle of restoring. Click HERE for a PowerPoint presentation of the project. Click HERE for a detailed breakdown of the internal forces in a editable Excel file.